Confocal sensors from Micro-Epsilon enable high-precision distance measurements, for example in industrial measurement tasks in semiconductor engineering and battery film production. With a large measuring range, a high linearity of < ± 1 micrometers…
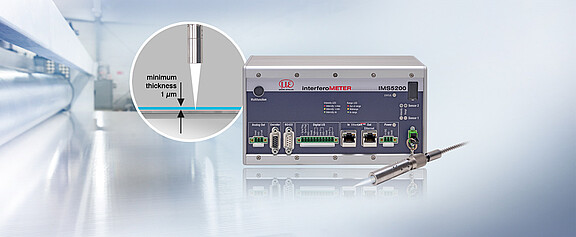
The new white light interferometers of the interferoMETER IMS5200-TH series are used for nanometer-precise coating thickness measurements from 1 to 100 micrometers. With a measuring rate of up to 24 kHz, the new white light interferometers are ideal…
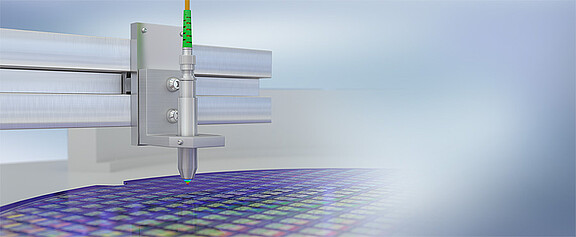
In the semiconductor industry, optics or aviation, measurements under vacuum conditions are part of everyday life, but also place the highest demands on sensor technology. Micro-Epsilon offers both catalog sensors and specially developed sensors that…