In the semiconductor industry, optics or aviation, measurements under vacuum conditions are part of everyday life, but also place the highest demands on sensor technology. Micro-Epsilon offers both catalog sensors and specially developed sensors that…
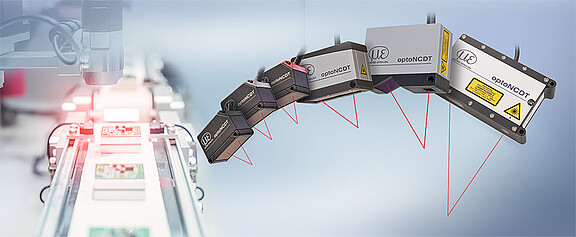
With the optoNCDT laser sensors, Micro-Epsilon offers a broad portfolio with measuring ranges from 2 to 1000 mm. This makes these sensors suitable for a variety of applications in a wide range of industries.
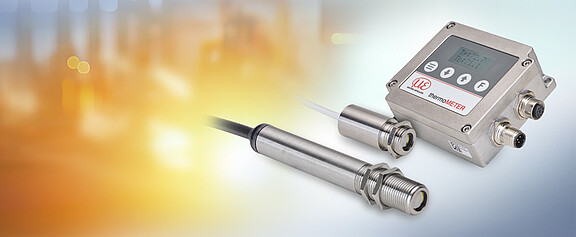
Three new pyrometers, the thermoMETER UC, SE and FI are designed for precise and stable temperature measurements in industrial processes. They offer first-class temperature compensation and signal quality, optimum adaptability for OEM series…