Precise sensor solutions for battery production
Modern batteries and accumulators are used in many different fields. Be it electric cars, energy storage devices, tools or smartphones – they will become ever more important in the future. A high level of automation as well as optimization of the individual manufacturing processes in battery production are required in order to constantly improve the quality, efficiency and economic viability of batteries. Micro-Epsilon offers precise sensors and measuring systems that perform in a wide range of measurement tasks for the many different manufacturing processes for electrodes, battery cells and battery modules.
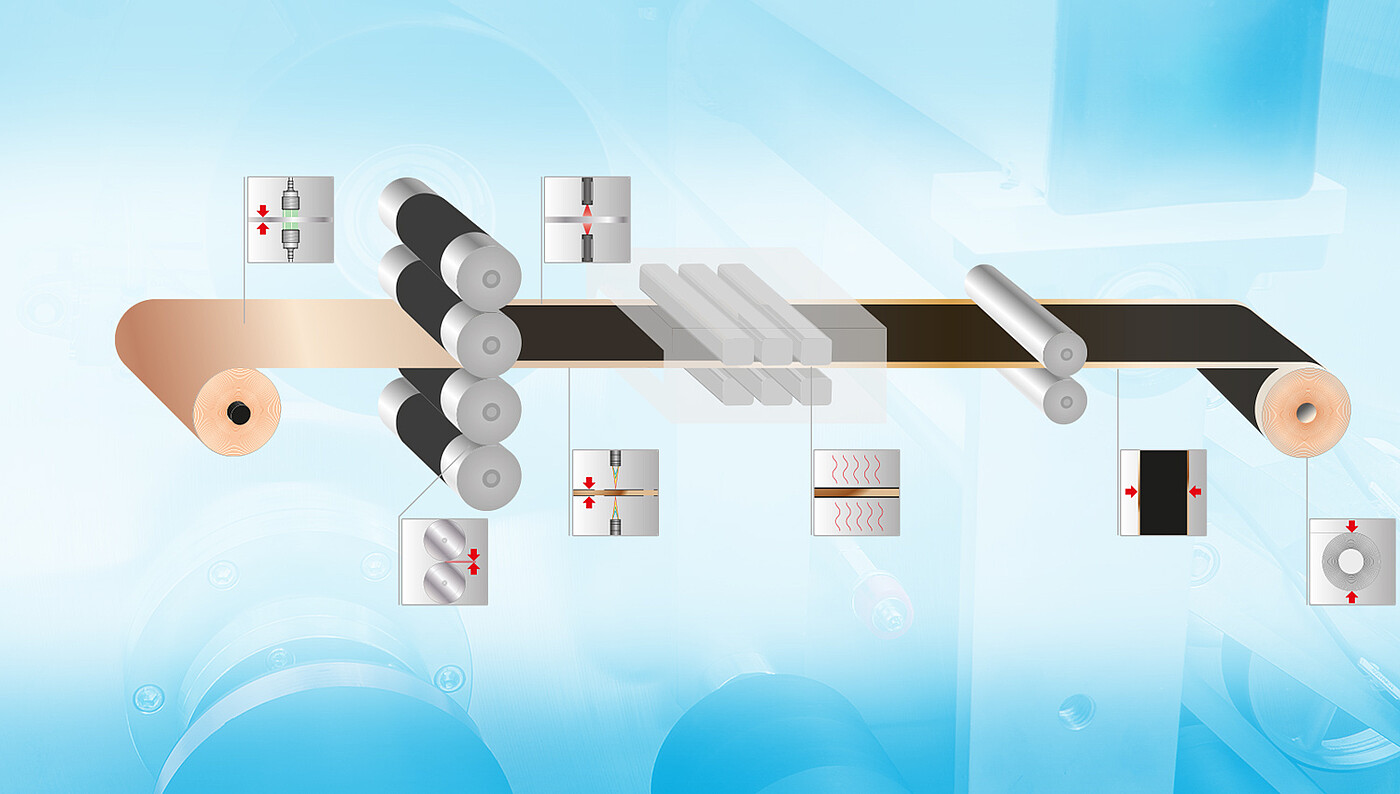
Why Micro-Epsilon?
- More precision and innovation – Made in Germany
- Hand in hand with our customers: quality and problem-solving expertise in series & OEM
- In-depth technological and practical knowledge in the field of battery manufacture
- Highly precise sensors and in-line measuring systems from a single source
Highly precise sensors for measuring the thickness of battery films
Non-contact displacement sensors from Micro-Epsilon offer numerous advantages in thickness measurement. Capacitive sensors, for example, have a relatively large measurement spot that compensates for inhomogeneous structures. Furthermore, capacitive sensors can be used at high temperatures. Thanks to integrated temperature compensation, the sensors deliver stable measurements in the submicrometer range and can also be used in drying processes.
In the case of optical thickness measurement, confocal chromatic sensors really come into their own, as do white light interferometers for the inline thickness measurement of battery films. The sensors are typically used to monitor and control wet coating processes, but are also suitable for dry coating processes.
You can be sure of the best sensor for the measurement task at hand, no matter what measuring object or type of coating (uncoated/coated) is involved. Just get in touch!
3D sensors and dimensional measurement technology for electrode and battery manufacture
3D sensors from Micro-Epsilon are used for assembly monitoring and for 3D inspection of coated films. 3D laser scanners are suitable for continuous strip inspection, while 3D snapshot sensors are used for stop-and-go measurements with exceptionally high precision. The 3D sensors by Micro-Epsilon allow for stable measurement with a high resolution and detect flaws on the smallest of shapes, such as spalling and inclusions. Optical micrometers that reliably check sheet travel are used to monitor the edges of strips.
Inline systems for measuring the thickness of battery films
thicknessGAUGE sensor systems are used to measure the thickness of strip materials in-line. Several models with different sensor types, measuring ranges and measuring widths are available for precise thickness measurement. The systems use two optical or electromagnetic distance sensors to measure the strip thickness of cell material, films and coatings with micrometers.
More precision for battery production
Micro-Epsilon offers the right solution for diverse battery production applications – from inline thickness measurement to precise machine monitoring to 3D surface inspection. The sensors are used by leading battery manufacturers and automotive companies around the world and impress thanks to their supreme precision and reliability.
You can find several application examples from the battery industry here